Harnessing the Power of Quality Automatic Capping in Your Manufacturing Process
Jul 21,2025
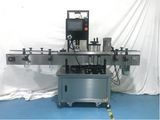
Harnessing the Power of Quality Automatic Capping in Your Manufacturing Process
Table of Contents
- 1. Introduction to Automatic Capping Machines
- 2. The Importance of Quality Capping in Manufacturing
- 3. Types of Automatic Capping Machines
- 3.1 Linear Capping Machines
- 3.2 Turret Capping Machines
- 3.3 Snap-on Capping Machines
- 3.4 Specialized Capping Machines
- 4. Benefits of Using Automatic Capping Machines
- 5. Key Considerations When Choosing a Capping Machine
- 6. Installation and Maintenance Best Practices
- 7. The Future of Automatic Capping Technology
- 8. Frequently Asked Questions
- 9. Conclusion
1. Introduction to Automatic Capping Machines
In the ever-evolving landscape of manufacturing, **automatic capping machines** have emerged as critical players in ensuring product integrity and operational efficiency. These machines are designed to apply caps to containers—be it bottles, jars, or other types of packaging—with precision and speed. By automating the capping process, manufacturers can significantly reduce labor costs, minimize human error, and enhance production rates.
This article delves into the ways that quality automatic capping can transform your manufacturing process, spotlighting its importance, types, benefits, and future trends.
2. The Importance of Quality Capping in Manufacturing
**Capping quality** is paramount in the packaging industry. It serves several key functions that directly affect product performance and consumer satisfaction:
1. **Seal Integrity**: A properly capped product ensures that contents remain fresh and protected from contaminants. This is particularly crucial for perishable goods, pharmaceuticals, and chemicals.
2. **Brand Protection**: Effective capping prevents spills and leakage, safeguarding your brand’s reputation by providing consumers with a reliable and high-quality product.
3. **Regulatory Compliance**: Many industries have specific capping standards that must be adhered to. Using quality capping solutions helps meet these regulatory requirements.
4. **Cost Efficiency**: Quality capping reduces product loss and minimizes returns due to packaging failures, directly impacting your bottom line.
By investing in high-quality automatic capping solutions, businesses can not only enhance their operational efficiency but also foster customer trust and loyalty.
3. Types of Automatic Capping Machines
Choosing the right type of **automatic capping machine** is essential for ensuring optimal performance in your manufacturing process. Here, we explore the various options available:
3.1 Linear Capping Machines
Linear capping machines operate by moving containers in a straight line through the capping process. This type is ideal for high-speed production lines, providing efficient capping for a variety of container shapes and sizes. They offer flexibility in capping different types of closures, from screw caps to flip-tops.
3.2 Turret Capping Machines
Turret capping machines utilize a rotating system to cap containers, making them suitable for medium to high-speed production. These systems are particularly effective for cylindrical containers and can handle multiple cap types. Their design allows for quick changeovers between different cap sizes.
3.3 Snap-on Capping Machines
Designed specifically for snap-on caps, these machines apply caps with a pushing mechanism, ensuring a secure fit. They are commonly used in the beverage and food industry, where quick service and efficient capping are essential.
3.4 Specialized Capping Machines
For industries requiring unique capping solutions, specialized machines are available. These can include custom systems designed to handle unique closure types or specific container shapes, ensuring that all packaging needs are met.
4. Benefits of Using Automatic Capping Machines
The integration of automatic capping machines into your manufacturing process can yield a multitude of advantages:
1. **Increased Production Speed**: Automating the capping process allows for faster speeds than manual methods, increasing overall output and reducing bottlenecks in production.
2. **Enhanced Precision and Consistency**: Automatic machines provide consistent torque and application, ensuring each cap is applied correctly every time, leading to fewer defects.
3. **Labor Cost Reduction**: With machines handling the capping process, businesses can reallocate labor resources to more critical tasks, thereby optimizing workforce efficiency.
4. **Improved Safety**: Automating capping reduces the risk of workplace injuries associated with manual capping processes, creating a safer working environment.
5. **Versatility**: Many automatic capping machines can be adjusted quickly for different cap sizes and container types, accommodating product line changes without significant downtime.
5. Key Considerations When Choosing a Capping Machine
Selecting the right **automatic capping machine** involves careful consideration of various factors:
1. **Production Volume**: Assess your production needs to determine the speed and capacity required from a capping machine.
2. **Type of Cap**: Different caps require specific capping machines, so identifying your cap type is crucial.
3. **Container Specifications**: Consider the size, shape, and material of your containers, as these factors can influence the choice of capping equipment.
4. **Budget**: Determine your budget for purchasing and maintaining capping machinery, ensuring that you account for both upfront costs and long-term operational expenses.
5. **Technical Support and Maintenance**: Choose a supplier that offers comprehensive support and maintenance services to keep your capping machine running smoothly.
6. Installation and Maintenance Best Practices
Proper **installation** and ongoing maintenance are essential for optimal performance of your automatic capping machines:
1. **Professional Installation**: Engage qualified technicians for installation to ensure that all components are set up correctly and efficiently.
2. **Regular Maintenance Checks**: Schedule routine maintenance to inspect and service your capping machinery, minimizing downtime and preventing costly repairs.
3. **Operator Training**: Train your staff on the proper operation of capping machines to enhance performance and safety.
4. **Monitoring Performance**: Use performance metrics to monitor the efficiency of your capping process, allowing for timely adjustments and improvements.
5. **Spare Parts Availability**: Establish a relationship with your supplier for the availability of spare parts to ensure quick replacements when necessary.
7. The Future of Automatic Capping Technology
As technology evolves, so too do automatic capping solutions. Emerging trends in the industry include:
1. **Smart Technology Integration**: The incorporation of IoT (Internet of Things) technology allows for real-time monitoring and adjustments, enhancing operational efficiency.
2. **Sustainability**: Manufacturers are focusing on eco-friendly capping solutions, with companies developing machines that utilize recyclable materials and reduce waste.
3. **Advanced Robotics**: Robotics and AI are set to transform capping processes, allowing for even greater precision and flexibility in production.
4. **Data Analytics**: Utilizing data analytics can provide insights into production performance, enabling manufacturers to make data-driven decisions for continuous improvement.
8. Frequently Asked Questions
1. What types of products benefit from automatic capping?
Most products in bottles or jars, including beverages, pharmaceuticals, and cosmetic products, can benefit from automatic capping.
2. How do I know which capping machine is right for my production line?
Consider your production volume, container specifications, and the type of cap you will be using. Consulting with a supplier can also help you choose the best option.
3. What maintenance is required for automatic capping machines?
Routine inspections, cleaning, lubrication of moving parts, and prompt replacement of worn components are essential for maintenance.
4. Can automatic capping machines handle different cap sizes?
Yes, many automatic capping machines are designed to be adjustable for different cap sizes and types.
5. What is the average cost of an automatic capping machine?
The cost can vary widely based on the type, size, and features of the machine. It's essential to consider both initial costs and long-term operational expenses.
9. Conclusion
Incorporating quality automatic capping machines into your manufacturing process can dramatically improve efficiency, consistency, and product integrity. By selecting the right machine tailored to your production needs, you can enhance operational workflows while reducing costs and ensuring regulatory compliance. As automatic capping technology continues to evolve, embracing these advancements will place your business at the forefront of the manufacturing industry, driving innovation and improving customer satisfaction. Investing in quality capping solutions today will pave the way for a successful and sustainable manufacturing operation for tomorrow.
Latest News
Discover Cutting-Edge Packaging Solutions at Booth B39
SANXIN MACHINERY – a leading innovator in packaging technology – cordially invites you to visit Booth B39 at the 4th Guiyang Pharmaceutical Machinery Exhibition (July 16–18, 2025, Guiyang International Convention & Exhibition Center).
Jul 11,2025
Invitation to Visit Sanxin Machinery at the 29th CBE China Beauty Expo
Invitation to Visit Sanxin Machinery at the 29th CBE China Beauty Expo
May 09,2025
Transparent box three-dimensional packaging technology has come to the fore
Transparent box three-dimensional packaging technology has come to the fore
Dec 27,2024