How to Optimize the Use of Automatic Shrink Wrap Machines in Production
Jul 10,2025
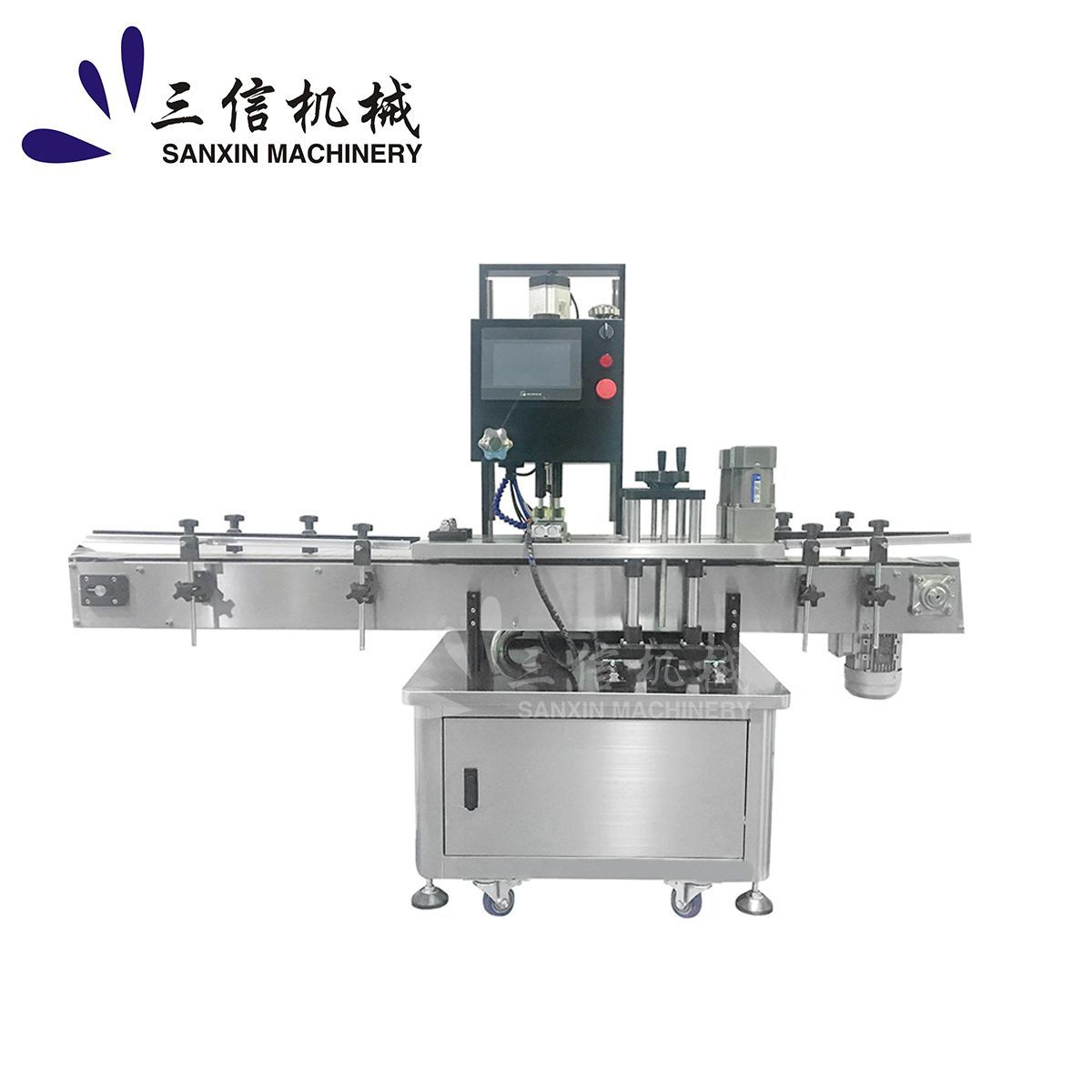
How to Optimize the Use of Automatic Shrink Wrap Machines in Production
Table of Contents
- Introduction to Automatic Shrink Wrap Machines
- Benefits of Using Automatic Shrink Wrap Machines
- Key Components of Shrink Wrap Machines
- Optimal Settings for Shrink Wrap Machines
- Maintaining Your Shrink Wrap Machine
- Common Issues and Troubleshooting
- Best Practices for Automatic Shrink Wrapping
- Future Trends in Shrink Wrapping Technology
- Conclusion
- FAQs
Introduction to Automatic Shrink Wrap Machines
In the fast-paced world of manufacturing, optimizing production processes is crucial to maintaining competitiveness and ensuring customer satisfaction. **Automatic shrink wrap machines** play a pivotal role in the packaging sector, offering efficiency and consistency that manual methods cannot match. These machines use heat to shrink a plastic film tightly around products, providing a secure, tamper-evident seal that enhances product integrity.
Understanding how to effectively utilize these machines can significantly streamline your manufacturing process. This article delves into various strategies to optimize the use of automatic shrink wrap machines, covering everything from initial setup to maintenance and troubleshooting.
Benefits of Using Automatic Shrink Wrap Machines
The adoption of automatic shrink wrap machines offers numerous advantages that can transform your production line. Here are some key benefits:
1. Enhanced Efficiency
Automatic shrink wrap machines can operate at high speeds, allowing for rapid packaging of products. This increased speed leads to higher output and reduced labor costs, freeing up resources for other critical tasks.
2. Improved Product Protection
Shrink wrapping provides a robust barrier against dust, moisture, and physical damage. This protective layer ensures that products maintain their quality throughout the supply chain, minimizing returns and enhancing customer satisfaction.
3. Consistency and Uniformity
Manual wrapping can lead to inconsistencies in packaging. Automatic machines ensure that each product is wrapped uniformly, which is essential for branding and professional presentation.
4. Space Efficiency
Many modern shrink wrap machines are designed to occupy minimal floor space while maximizing output. This space-saving design is ideal for production facilities with limited room.
5. Flexibility for Various Products
Automatic shrink wrap machines can adapt to different product sizes and shapes, making them versatile for various industries, including food, cosmetics, and pharmaceuticals.
Key Components of Shrink Wrap Machines
To optimize the use of shrink wrap machines, it’s essential to understand their key components:
1. Film Dispenser
This component supplies the shrink film that encases the product. Choosing the right type of film is crucial for achieving the desired results.
2. Sealing Mechanism
The sealing mechanism creates the necessary seals on the film to secure the product. This part is pivotal in ensuring that the seal is tight and reliable.
3. Heating Element
The heating element is responsible for shrinking the film around the product. Proper calibration of the temperature is essential to avoid over or under-shrinking.
4. Control Panel
The control panel allows operators to set parameters for speed, temperature, and sealing settings. Familiarity with this panel is essential for efficient operation.
Optimal Settings for Shrink Wrap Machines
Setting up your automatic shrink wrap machine correctly is crucial for optimal performance. Here are some important settings to consider:
1. Temperature Settings
The temperature should be adjusted based on the type of shrink film used. A general rule is to start with the manufacturer’s recommendations and fine-tune based on the results.
2. Speed Settings
Finding the right speed is essential. Too fast can result in improper seals, while too slow can hinder production efficiency. Testing different speeds can help identify the optimal setting.
3. Film Tension
Proper film tension ensures a snug fit around the product without excessive force that could damage delicate items. Adjust the tension settings based on the size and weight of the products being wrapped.
Maintaining Your Shrink Wrap Machine
Regular maintenance of your shrink wrap machine is necessary to prevent unexpected downtime and ensure long-term efficiency. Here are some maintenance tips:
1. Daily Cleaning
At the end of each production day, clean the machine to remove any residual film and contaminants. This practice helps prevent jams and maintains the machine’s performance.
2. Lubrication
Regular lubrication of moving parts is essential to keep the machine running smoothly. Refer to the manufacturer’s guidelines for recommended lubricants and intervals.
3. Inspection of Components
Routine inspections of the film dispenser, sealing mechanism, and heating elements can help identify wear and tear before they escalate into major issues.
Common Issues and Troubleshooting
Even the most advanced machines can encounter issues. Being proactive can mitigate these problems:
1. Film Jamming
Film jams are one of the most common issues. Regular cleaning and proper adjustments to the film tension can often resolve this problem.
2. Inconsistent Sealing
If seals are inconsistent, check the sealing temperature and pressure settings. Adjusting these can often improve seal quality.
3. Under or Over Shrinking
If products are either under or over-shrunk, recalibrating the heating element’s temperature or speed settings may be necessary.
Best Practices for Automatic Shrink Wrapping
Following best practices ensures that your shrink wrapping process is efficient and effective:
1. Conduct Regular Training
Ensure that all operators are trained on the machine’s features and troubleshooting techniques. This knowledge can prevent minor issues from escalating.
2. Use Quality Materials
Investing in high-quality shrink film and machine components will lead to better performance and durability. Quality materials enhance the overall effectiveness of the shrink wrap process.
3. Continuous Monitoring
Implement a system for continuous monitoring of machine performance and product quality. Regular checks allow for timely adjustments and maintenance.
Future Trends in Shrink Wrapping Technology
As technology evolves, the shrink wrapping industry is also advancing. Here’s what to expect in the future:
1. Increased Automation
The future will likely see more automated solutions, integrating artificial intelligence and machine learning to enhance efficiency and reduce errors.
2. Eco-Friendly Materials
With a growing emphasis on sustainability, the industry is moving towards biodegradable and recyclable shrink films, reducing environmental impact.
3. Smart Technology Integration
The incorporation of IoT devices will allow for real-time monitoring and analytics, optimizing production processes further and improving maintenance practices.
Conclusion
Optimizing the use of automatic shrink wrap machines is crucial for enhancing productivity, reducing costs, and ensuring product quality in manufacturing processes. By understanding the machine's components, maintaining optimal settings, and adhering to best practices, businesses can significantly improve their packaging efficiency.
Continuous evolution in technology and materials will further refine the shrink wrapping process, paving the way for more sustainable and efficient solutions. Embracing these changes will empower manufacturers to stay ahead of the competition and meet the growing demands of the market.
FAQs
1. What is the purpose of automatic shrink wrap machines?
Automatic shrink wrap machines provide a secure and protective seal around products, enhancing their integrity and presentation during storage and transportation.
2. How often should I maintain my shrink wrap machine?
Regular maintenance should be conducted daily, with more in-depth inspections and lubrication scheduled weekly or bi-weekly depending on usage.
3. Can I use different types of shrink film?
Yes, but it’s essential to adjust the machine settings according to the specifications of the film type to ensure optimal performance.
4. What are common problems with shrink wrap machines?
Common issues include film jamming, inconsistent sealing, and under or over shrinking, which can often be resolved with proper adjustments and maintenance.
5. How can I improve the efficiency of my shrink wrapping process?
Investing in quality materials, training operators, and implementing continuous monitoring systems can significantly enhance the efficiency of the shrink wrapping process.
Latest News
Discover Cutting-Edge Packaging Solutions at Booth B39
SANXIN MACHINERY – a leading innovator in packaging technology – cordially invites you to visit Booth B39 at the 4th Guiyang Pharmaceutical Machinery Exhibition (July 16–18, 2025, Guiyang International Convention & Exhibition Center).
Jul 11,2025
Invitation to Visit Sanxin Machinery at the 29th CBE China Beauty Expo
Invitation to Visit Sanxin Machinery at the 29th CBE China Beauty Expo
May 09,2025
Transparent box three-dimensional packaging technology has come to the fore
Transparent box three-dimensional packaging technology has come to the fore
Dec 27,2024